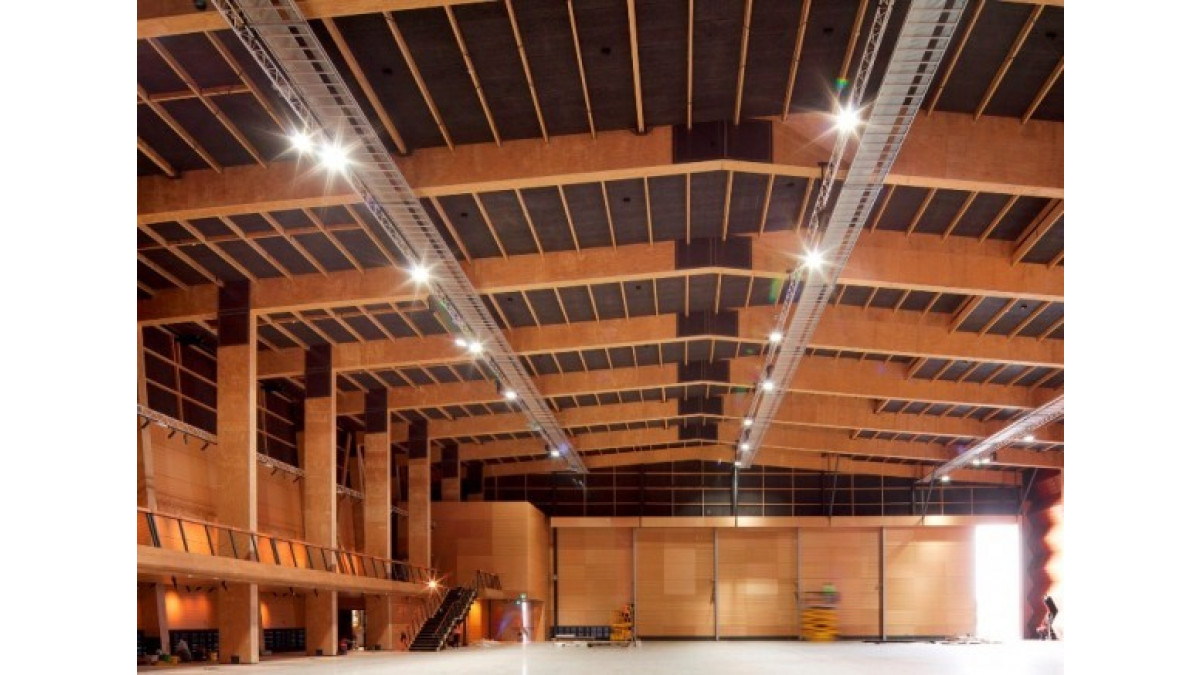
When embarking on a construction project, one of the key components that can dramatically affect your overall budget is the cost of formwork. Laminated Veneer Lumber (LVL) timber formwork, in particular, has gained popularity due to its strength and versatility. Understanding how to calculate its prices can save you significant costs and prevent budget overruns. In this guide, we will explore various aspects of LVL timber formwork and provide you with a step-by-step approach to estimating its costs effectively.
Understanding LVL Timber Formwork
Before jumping into calculations, it’s essential to grasp what LVL timber formwork is. Laminated Veneer Lumber is an engineered wood product made by bonding layers of wood veneers together with adhesive. This composite construction creates a material that is not only stronger than traditional wood but also more resistant to warping and shrinking. The process of creating LVL involves carefully selecting high-quality veneers, which are then layered and glued under heat and pressure, resulting in a product that boasts enhanced structural integrity and longevity.
What is LVL Timber Formwork?
LVL timber formwork is primarily used in construction projects as a supportive structure for concrete. It serves as a mold into which concrete can be poured, helping it to take on the desired shape as it sets. The strength and stability of LVL make it a reliable choice for various applications, including foundations, walls, and beams. Additionally, LVL can be customized to fit specific project requirements, allowing for intricate designs and unique architectural features. This adaptability makes LVL an increasingly popular choice among architects and builders alike.
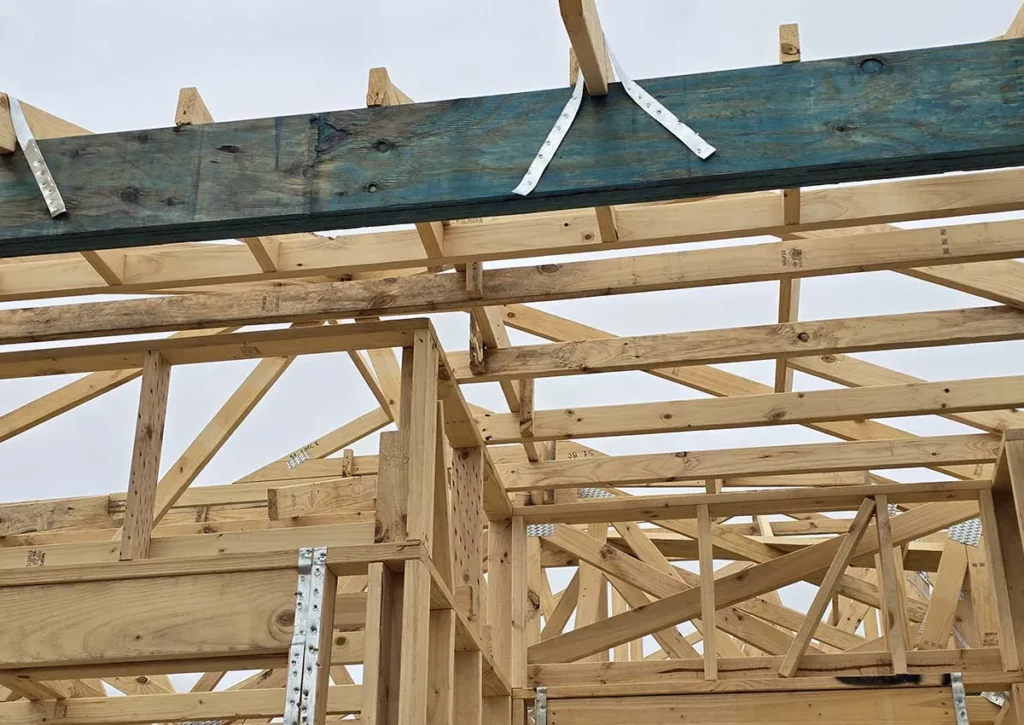
Benefits of Using LVL Timber Formwork in Construction
The use of LVL timber formwork offers several key benefits:
- Durability: LVL is engineered to last, reducing the frequency of repairs and replacements.
- Weight: Compared to other materials, LVL is lightweight, making it easier to handle and install.
- Consistency: The engineered nature of LVL ensures a uniform quality, minimizing the variations found in natural wood.
- Cost-Effective: While the upfront cost may be higher, its durability and efficiency often lead to lower overall project costs.
Moreover, LVL timber formwork is also environmentally friendly. As it is made from renewable resources, it contributes to sustainable building practices. The manufacturing process of LVL utilizes wood that might otherwise be considered waste, allowing for a more efficient use of forest resources. Additionally, many manufacturers are now adopting eco-friendly adhesives and practices, further enhancing the sustainability of LVL products. This makes LVL not only a practical choice for construction but also a responsible one, appealing to environmentally conscious builders and developers.
Another significant advantage of LVL timber formwork is its resistance to moisture and pests. Unlike traditional timber, which can be susceptible to rot and insect damage, LVL is treated during its production process to withstand these common issues. This characteristic is particularly beneficial in regions with high humidity or where pest infestations are prevalent. By using LVL, contractors can ensure the longevity and reliability of their formwork, ultimately leading to safer and more durable structures.
Read about lvl consruction on: Why LVL Construction Materials Are a Game Changer for the Building Industry
Factors Influencing LVL Timber Formwork Prices
Calculating the price of LVL timber formwork requires an understanding of several factors that can influence the overall costs. Here are the primary considerations that must be taken into account.
Material Quality and Its Impact on Price
The quality of the LVL timber significantly affects its price. Higher-grade LVL timber possesses better structural integrity and is less likely to warp, rot, or fail under pressure. It’s important to assess your project needs: while cheaper options might save you money initially, they could lead to more expenses down the line due to replacements or repairs. Additionally, higher-quality LVL timber often comes with better warranties and guarantees, providing peace of mind that can be invaluable for large-scale projects. Investing in premium materials can also enhance the overall aesthetic of the construction, ensuring that the finished product meets both functional and visual standards. Read more about pressure on https://www.princeton.edu/~asmits/Bicycle_web/pressure.html
Market Trends and Price Fluctuations
The cost of materials can fluctuate based on market trends. Factors such as demand, production costs, and availability can lead to sudden changes in pricing. Staying updated on market conditions can help you budget more accurately and make informed purchasing decisions. Furthermore, geopolitical factors and environmental regulations can also play a significant role in the timber market. For instance, restrictions on logging in certain regions can lead to scarcity, driving prices up. Understanding these dynamics can empower builders and contractors to time their purchases strategically, potentially saving substantial amounts on their projects. Engaging with suppliers who have a finger on the pulse of the market can also provide valuable insights into when to buy and what materials may be worth investing in for future projects.
Step-by-Step Guide to Calculating LVL Timber Formwork Prices
Now that we’ve discussed the basics and influencing factors, let’s dive into the calculation process. This step-by-step guide will help streamline your budgeting for LVL timber formwork.
Estimating the Quantity of LVL Timber Required
The first step in your cost calculation is determining how much LVL timber is needed for your project. This will involve:
- Measuring the dimensions of the area that requires formwork.
- Calculating the volume of concrete to be poured to understand how much formwork is necessary.
- Determining the specific LVL sizes and lengths required based on your design.
It’s important to remember that LVL timber comes in various thicknesses and grades, which can affect both strength and cost. Therefore, consulting with a structural engineer can be beneficial to ensure that the selected LVL is appropriate for the load it will bear. Additionally, considering the layout of your formwork can help minimize waste and optimize the use of materials, ultimately leading to more accurate budgeting. Click here to find more about thicknesses.
Incorporating Labor and Other Costs
Once you have estimated the quantity of LVL timber required, the next step is to consider the ancillary costs:
- Labor costs associated with the installation of the formwork.
- Transportation costs for bringing materials to the construction site.
- Additional equipment rental if needed for installation.
All these factors contribute to the total estimate, so ensure you include them in your budget considerations. Moreover, it’s wise to account for potential delays or unforeseen circumstances that could affect labor efficiency, such as weather conditions or site accessibility issues. Keeping a contingency fund within your budget can provide a safety net for such occurrences, allowing your project to stay on track without financial strain.
Tips for Budgeting Your Construction Job
Creating a budget for your construction job involves more than just tallying lumber costs. Here are a few practical tips to help you manage your finances effectively.
How to Save on LVL Timber Formwork Costs
There are several strategies to reduce your overall costs:
- Shop around for suppliers, as prices can vary significantly.
- Consider buying in bulk, as discounts may be available for larger orders.
- Reuse formwork when possible, especially if you have projects lined up in the future.
Planning for Unexpected Expenses
Finally, always include a contingency in your budget for unexpected costs. Construction projects can be unpredictable, so setting aside a percentage of your budget for unforeseen expenses can provide peace of mind. A good rule of thumb is to allocate about 10-15% of the total budget for contingencies.
Conclusion: Making Smart Decisions with LVL Timber Formwork Pricing
Calculating LVL timber formwork prices effectively requires understanding the material, accounting for a variety of influencing factors, and following a structured approach to estimating costs. By implementing careful planning and budgeting practices, you can manage your construction budget more efficiently and make informed decisions that contribute to the project’s overall success.
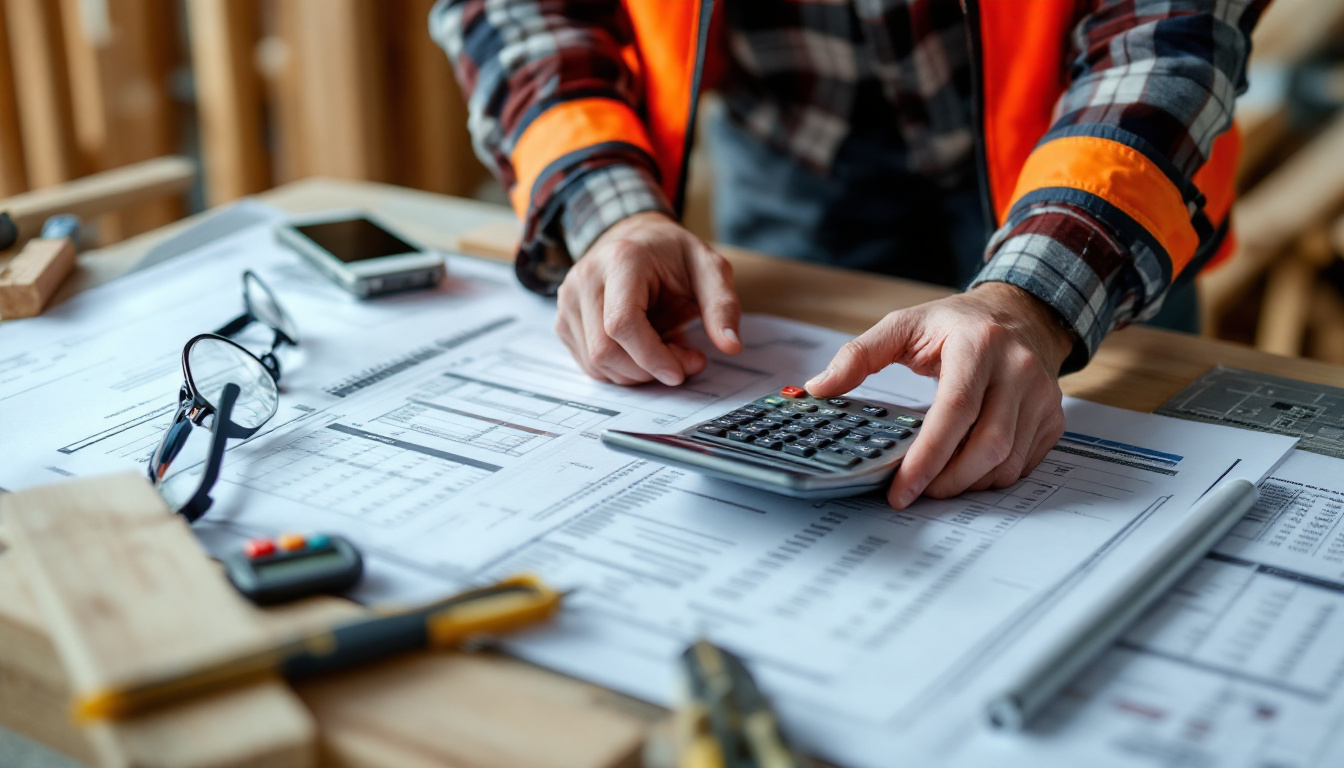
Armed with this information, you’re now ready to tackle your next construction job with confidence, ensuring you get the best value during your LVL timber formwork procurement.